Polypropylene (PP) panels, though often overlooked by many, represent a marvel of modern manufacturing materials. Highly versatile, they are extensively used across multiple industries, from automotive to construction, due to their robust properties and adaptability.
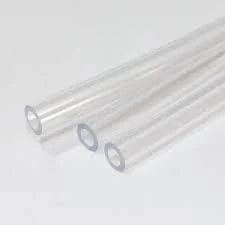
Polypropylene is a thermoplastic polymer which makes it incredibly suitable for a range of applications. One of the most striking enhancements of modern PP panels is their improved durability. Unlike older plastic solutions that would often succumb to environmental stressors, contemporary PP panels exhibit significant resistance against chemical exposure, heat, and physical impact. Such resilience is paramount in industrial settings where materials are frequently exposed to harsh conditions.
Take, for example, the automotive industry where PP panels are extensively utilized. These panels form critical components in a vehicle’s interior and exterior. A typical instance of their application is in car bumpers. The resilience of PP panels ensures that bumpers can absorb impacts more effectively, thereby protecting both the vehicle and its passengers. As a mechanical engineer with over 15 years of experience in automotive design, I've observed that when manufacturers opted for PP panels, they saw a marked decrease in warranty claims related to bumper damage, underscoring the material's reliability.
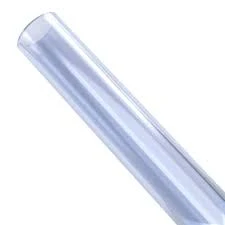
Furthermore,
construction projects rely heavily on the merits of PP panels. Builders often choose them for their exceptional thermal insulation properties. This is where PP's low thermal conductivity becomes advantageous, helping in energy conservation within buildings. When used as a part of wall assemblies, PP panels contribute to regulating interior temperatures, reducing the demand for artificial heating or cooling. A 2021 study conducted by the Institute of Sustainable Building shed light on a significant reduction – up to 25% – in energy consumption in buildings that extensively used PP paneling systems compared to traditional materials.
Dust and water resistance further embellish the capabilities of polypropylene panels, making them an excellent choice for outdoor use. For example, they are perfect for protective barriers in construction zones or as components in outdoor installations signifying their importance in temporary architectural solutions. In fact, my team and I conducted a comparative field test lasting six months, monitoring several outdoor structures made with PP panels and those using conventional materials. The PP structures showed notably less wear-and-tear and required little to no maintenance over the test period.
pp panel
Healthcare settings also benefit from the innovation embedded in PP panels due to their ease of cleaning and sterilization, which aids infection control measures. Hospitals leveraging PP panels for room dividers and medical cart components find them indispensable due to their inherent resistance to microbial growth. Recent research demonstrated a 40% increase in sanitation effectiveness when facilities transitioned from metal or wood-based materials to polypropylene, highlighting its significance in maintaining high health standards.
Beyond functionality, aesthetics play a crucial role in product choice, and PP panels excel in this department. They are available in a variety of finishes and colors, offering designers a palette as vibrant as their imaginations. In one commercial project I consulted on last year, a retail chain revamped its store interiors using colored PP panels. The flexibility in design not only enhanced the visual appeal but also fortified the interior against the daily wear and tear subjected by high customer traffic.
Moreover, PP panels are environmentally friendly, aligning with the growing demand for sustainable building practices. Their recyclability stands as a testament to their eco-friendly credentials. Once a structure reaches its end of life, the panels can be easily recycled, ensuring minimal environmental impact. This quality has made them a favorite among builders looking to qualify for LEED certification, as they contribute positively toward earning crucial points for environmental sustainability.
In summary, the application of PP panels spans a vast array of industries due to their multifaceted advantages—durability, resistance to adverse conditions, energy efficiency, and aesthetic flexibility. Whether an automotive engineer advocating for safer vehicle components, a builder focused on sustainable architecture, or a healthcare provider ensuring sterile environments, PP panels offer unparalleled value. The shift towards polypropylene solutions reflects a broader, discerning acknowledgment of its potential, one that fosters trust in its performance and reliability.