High-Density Polyethylene (HDPE) sheets have become an indispensable component across various industries, thanks to their remarkable properties and versatility. One of the critical factors to consider when working with HDPE sheets is their thickness, as it directly impacts the material's performance in specific applications. This comprehensive exploration into HDPE sheet thickness seeks to provide valuable insights from real-world experiences, expert evaluations, authoritative recommendations, and trustworthy guidelines to help you make informed decisions.
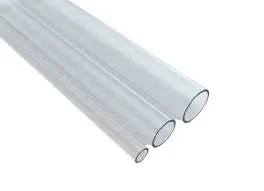
HDPE sheets are renowned for their impressive durability, chemical resistance, and impact strength, making them a popular choice for applications ranging from food packaging to industrial flooring. However, the sheet's thickness plays a pivotal role in determining its suitability for particular uses. For instance, thinner HDPE sheets, typically ranging from 0.5 mm to 2 mm, tend to be more flexible and are often used in applications where lightweight and pliability are crucial, such as liners in agriculture or landfill covers. On the other hand, thicker sheets, which can range from 10 mm to 100 mm or more, offer enhanced rigidity and strength, making them ideal for heavy-duty applications like marine construction or industrial machining.
From an expertise standpoint, selecting the right HDPE sheet thickness involves understanding the environmental and mechanical stresses the material will face. Thicker sheets undoubtedly offer superior load-bearing capacity and resistance to wear and tear, which is why they are preferred for applications that demand a higher level of durability. Experts recommend a thorough evaluation of the operational environment, including temperature variations and exposure to chemicals, to determine the optimal thickness. For instance, in cold storage applications, thick HDPE sheets are preferred because they exhibit minimal thermal expansion and contraction, ensuring dimensional stability and longevity.
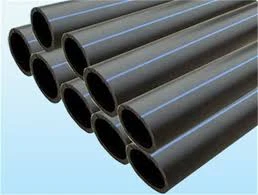
Authoritative bodies in material science provide standardized guidelines to help in the selection process of HDPE sheet thickness. These standards often take into account factors such as tensile strength, elasticity, and thermal stability. By adhering to these guidelines, industries can ensure not only the safety and efficacy of their applications but also compliance with regulatory requirements. This is particularly important in food and pharmaceutical industries where material choice can impact product safety and integrity.
hdpe sheet thickness
Trustworthiness is paramount when procuring HDPE sheets, as the market is flooded with variations that may not meet the rigorous demands of certain applications. Engaging with reputable manufacturers or suppliers, who have a proven track record and offer certification for their products' specifications, can alleviate concerns regarding quality and performance. Transparency about the production process and adherence to industry standards are indicators of a trustworthy partner in your material sourcing journey.
Investing in the right HDPE sheet thickness can lead to cost savings in the long term. While thicker sheets may entail a higher initial investment, their durability and resistance to environmental degradation often result in reduced maintenance and replacement costs. This not only ensures a sustainable operation but also maximizes the return on investment.
In conclusion, the significance of selecting the appropriate HDPE sheet thickness cannot be overstated. By focusing on the specifics of your application, consulting with experts, adhering to authoritative guidelines, and maintaining high standards of trustworthiness in procurement, you can optimize both performance and cost-effectiveness. This approach not only leverages the strengths of HDPE sheets but also harnesses their full potential across diverse industrial landscapes.