Selecting the right welding rod is crucial for ensuring the strength and durability of your welded joints. Welding rods, also known as filler metals, play a pivotal role in binding two or more metals during the welding process. With a plethora of options available, choosing the ideal welding rod involves examining several key factors, including materials, applications, and skill level.
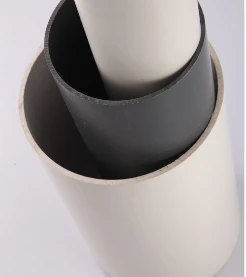
For beginners and seasoned professionals alike, understanding the specific composition and function of welding rods can significantly enhance the quality of the welds produced. When welding steel, for instance, considering the type of steel—be it carbon steel or stainless steel—determines the appropriate welding rod. Carbon steel often pairs well with mild steel welding rods due to their compatibility in composition and melting points. On the other hand, stainless steel might necessitate chromium and nickel-based rods to prevent corrosion and ensure a robust bond.
Welders should also take into account the welding position. Some rods are designed for all-position welding, allowing for greater flexibility when tackling complex projects. For instance, the E6010 and E6011 rods are versatile enough to be used in flat, horizontal, vertical, and overhead positions, making them ideal for challenging environments and construction projects. This versatility further extends the applicability of certain rods, thus influencing their popularity among professional welders.
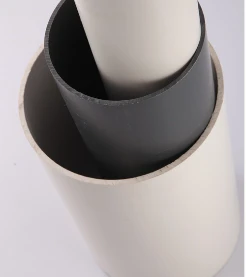
Moreover, the selection of AC or DC current in welding machines also influences rod selection. Some rods work best with alternating current, while others are more suited to direct current. Understanding your equipment’s capabilities and limitations is essential for pairing it with the right rod, which directly impacts the structural integrity of your welds.
welding rod
Quality in welding isn’t solely dependent on technical specifications. The environment in which the welding takes place can heavily affect performance. For instance, moisture can lead to hydrogen inclusion in the weld, a common cause of weld failure. Selecting a rod with moisture-resistant coatings can mitigate these risks, boosting both trustworthiness and the longevity of the welded structure.
Skilled welders know the significance of rod diameter in relation to the thickness of the materials being joined. A thicker material necessitates a larger diameter rod to achieve adequate penetration and bonding of the metals. Conversely, thinner materials require smaller diameter rods to prevent burn-through and achieve a smooth finish. This expertise and meticulous attention to detail are what differentiate excellent welds from merely adequate ones.
For authority on this subject, consulting welding standards and guidelines from organizations such as the American Welding Society (AWS) provides reliable insights into choosing the right welding rod. These bodies conduct rigorous testing and offer impartial, expert-backed recommendations that can greatly enhance a welder’s knowledge base and practical outcomes.
Ultimately, the choice of welding rod is a strategic decision that blends technical knowledge, environmental awareness, and practical application. By leveraging experience and expert resources, welders can make informed decisions that enhance trust in their workmanship and ensure the safety and reliability of their projects over time. Such careful selection not only boosts operational efficiency but also cultivates a professional reputation for quality, contributing to long-term success in the welding industry.