Plastic welding rods play a crucial role in the field of plastic fabrication and repair. These specialized rods are designed to facilitate the joining of plastic materials, ensuring structural integrity and durability. The key to effectively using plastic welding rods lies in understanding their various applications, materials, and techniques.
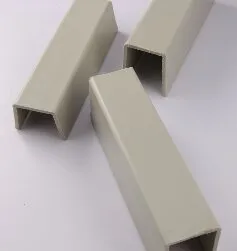
An important aspect of plastic welding rods is their material composition. These rods are crafted from different types of plastic, each suited for specific applications. Common materials include Polypropylene (PP), Polyethylene (PE), and Polyvinyl Chloride (PVC), among others. Each material possesses unique properties – for instance, PP is known for its resistance to chemicals and fatigue, making it ideal for chemical tanks and automotive components. Meanwhile, PE finds use in joinery for water pipes due to its excellent moisture resistance and flexibility.
Selecting the right plastic welding rod involves evaluating factors such as the type of plastic being welded, the desired strength of the joint, and the environment in which the welded part will function. Experience shared by professionals underscores the importance of ensuring compatibility between the welding rod and the base material. Mismatched materials can lead to joint failures, which can compromise the entire structure.
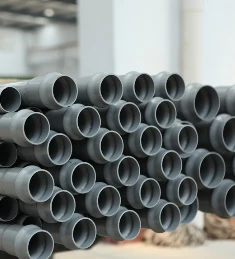
The expertise in using plastic welding rods extends to the method of application. Different welding techniques like hot air welding, extrusion welding, and injection welding require specific skills and equipment. Hot air welding, for example, uses a stream of hot air to melt the rod and the base material, allowing them to fuse. This technique is favored for its precision and control, making it ideal for intricate parts like semiconductors and intricate laboratory equipment.
In extrusion welding, a welding gun is used to extrude the molten rod onto the joint. This method is particularly useful for larger, industrial applications. Professionals stress the importance of controlling the temperature and flow rate during this process to avoid defects such as voids or weak spots.
plastic welding rod
A crucial point of authoritativeness is the adherence to industry standards and certifications. High-quality plastic welding rods typically comply with certifications such as ASTM (American Society for Testing and Materials) standards that govern material specifications and welding procedures. Compliance ensures that the welding rods meet the stringent criteria for safety and reliability, lending credibility and trustworthiness to the product.
Moreover, trusted manufacturers often provide detailed guidelines and training on the use of their products. This information is invaluable for both novices and experienced practitioners aiming to optimize their welding processes. The consistency and reliability of welding rods from reputable sources contribute significantly to the trust they earn in their performance.
The field also necessitates a commitment to ongoing education and adaptation to technological advancements. Emerging trends focus on enhancing the environmental sustainability of plastic welding materials. This involves exploring biodegradable options and improving recycling capabilities, reflecting a growing concern for environmentally friendly manufacturing practices.
The trustworthiness of information regarding plastic welding rods can be further bolstered by case studies and user testimonials. Case studies that highlight successful applications of plastic welding rods in critical projects can serve as a reliable reference for new users. Similarly, testimonials from seasoned professionals in the field can offer insights into real-world experiences and best practices.
In conclusion, plastic welding rods are integral to the successful joining of plastic components across various industries. Their selection and use demand a deep understanding of material properties, welding techniques, and industry standards. By focusing on compatibility, trusted sourcing, and adherence to best practices, professionals can ensure the reliability and durability of plastic welds. As the industry evolves, embracing technological advancements and sustainable practices will further enhance the expertise and trustworthiness associated with plastic welding.