Plastic welding rods have emerged as an essential component in the plastic fabrication industry due to their versatility and reliability in joining thermoplastic materials. These cylindrical tools play a crucial role in processes that range from simple repairs to complex industrial applications. To fully understand the impact and utility of plastic welding rods, it's imperative to delve deep into their physical properties, applications, and the technological advancements that make them indispensable today.
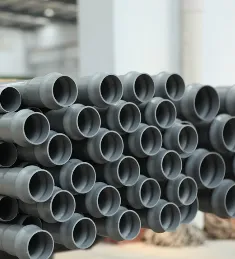
Plastic welding rods are crafted from various thermoplastic materials such as PVC, polypropylene, polyethylene, and ABS, each offering distinct characteristics tailored to specific welding requirements. The selection of the appropriate welding rod material is critical, as it must match the type of plastic material being welded to ensure strong, durable bonds. For instance, a PVC welding rod is ideal for joining PVC sheets and pipes, often used in plumbing and chemical processing due to its resistance to corrosion and chemical aggression.
Experience in utilizing plastic welding rods reveals that mastering the technique of plastic welding is as crucial as selecting the correct rod material. Skilled technicians know that maintaining consistent heat and speed while applying welding rods determines the quality of the weld. Too much heat can cause the rod to burn or the base material to degrade, whereas insufficient heat may lead to weak bonds. Expertise in this area often involves hands-on practice, as understanding the nuances of different material behaviors under heat is acquired through experience.
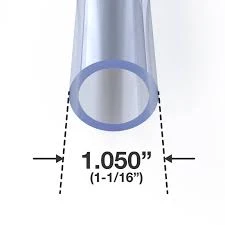
The process of plastic welding using these rods involves either hot air or extrusion welding methods. Hot air welding employs a hand-held heat gun with a nozzle that directs hot air onto the application area. This technique demands precision, as the temperature typically ranges between 200°C to 300°C. The welding rod is then fed alongside the base materials, forming a molten pool that cools down to create a seamless bond. On the other hand, extrusion welding involves a processing unit that simultaneously heats and extrudes the welding rod onto the seams. This method is particularly favored in larger-scale applications due to its efficiency and the strength of the resulting joints.
From an expertise perspective, understanding the mechanics of plastic fusion is fundamental. It's essential to recognize how thermal expansion and contraction affect the integrity of the bond. Technicians with an authoritative grasp of plastic welding are capable of predicting potential failure points and reinforcing them preemptively. This forward-thinking approach not only saves time and resources but also enhances the longevity of the welded structures.
plastic welding rod
Numerous industries, from automotive to construction, rely on plastic welding rods for their lightweight and corrosion-resistant properties. They are used in fabricating water tanks, piping systems, and even vehicle components where metal alternatives are unsuitable due to weight constraints or corrosion susceptibility. As the drive for sustainability intensifies, the recycling and repair of plastic products gain more emphasis. Plastic welding rods facilitate the repair of plastic items, reducing landfill waste and promoting the circular economy model.
Trustworthiness in the use of plastic welding rods stems from adhering to industry standards and certifications. The reliability of these rods is often certified by regulatory organizations, ensuring that they meet stringent safety and performance benchmarks. Moreover, manufacturers of high-quality welding rods provide technical support and comprehensive guides to assist users, ensuring that proper procedures are followed, and optimal results are achieved.
Innovation plays a pivotal role in the evolution of plastic welding rods. Today, advancements in material science contribute to the development of rods that offer enhanced strength, flexibility, and stability under a variety of environmental conditions. This continuous improvement aligns with the need for solutions that support advanced manufacturing processes and applications.
In conclusion, plastic welding rods are more than just auxiliary materials in plastic joining operations. They are pivotal in ensuring the durability and longevity of thermoplastic products across various industries. Understanding their properties and mastering their application underpins successful plastic welding endeavors. As technology advances, the capabilities of these rods continue to expand, reaffirming their importance in both current and future manufacturing landscapes.