The Pivotal Role of Perforated HDPE Pipes in Modern Infrastructure
High-Density Polyethylene (HDPE) pipes, with their perforated design, have emerged as a game-changer in various engineering and construction applications. Known for their durability, chemical resistance, and cost-effectiveness, these pipes have found extensive use in sectors ranging from agriculture to waste management.
Perforated HDPE pipes, as the name suggests, are HDPE pipes with strategically placed holes along their length. These perforations are precisely engineered to allow controlled flow of liquids or gases, making them ideal for drainage systems, leach fields, and even water treatment plants. The percentage of the pipe surface that is perforated can vary according to specific project requirements, hence the term perforated hdpe pipe.
The primary advantage of perforated HDPE pipes lies in their robustness. HDPE material, being highly resistant to corrosion and impact, ensures a long service life even under harsh conditions. Moreover, their flexibility allows for bending without compromising structural integrity, thus adapting well to uneven terrain or subterranean shifts.
In agricultural settings, perforated HDPE pipes are often used for subsurface irrigation, ensuring efficient water distribution while minimizing evaporation losses. They also find application in stormwater management, where they facilitate the controlled infiltration of rainwater into the ground, reducing flooding risks and replenishing groundwater reserves.
In environmental engineering, perforated HDPE pipes are integral to landfill liner systems, enabling the safe extraction of leachate
In environmental engineering, perforated HDPE pipes are integral to landfill liner systems, enabling the safe extraction of leachate
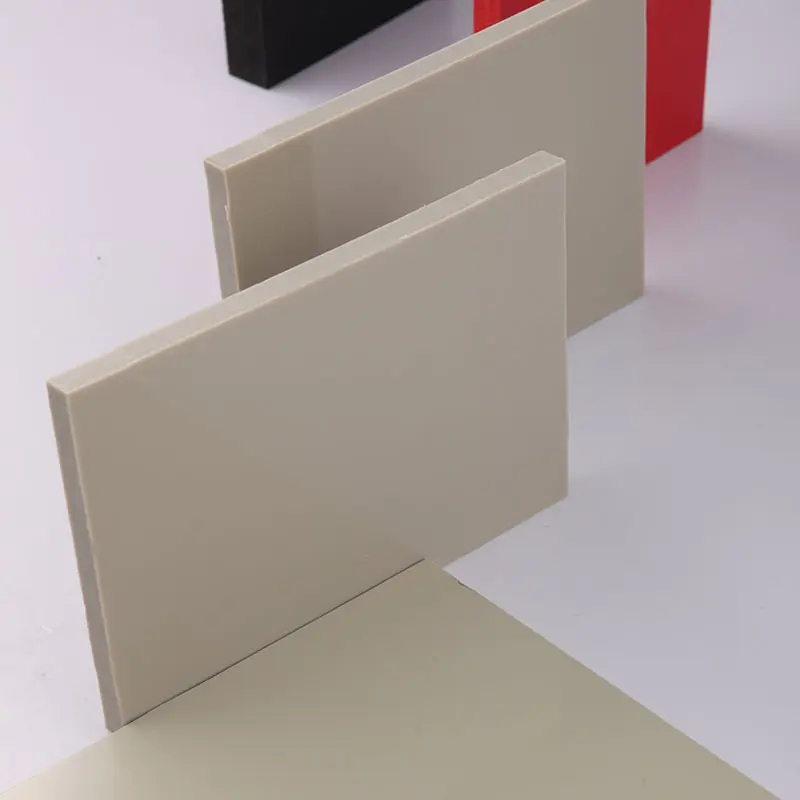
In environmental engineering, perforated HDPE pipes are integral to landfill liner systems, enabling the safe extraction of leachate
In environmental engineering, perforated HDPE pipes are integral to landfill liner systems, enabling the safe extraction of leachate
perforated hdpe pipe. They are also used in bioremediation processes, allowing air or nutrients to penetrate contaminated soil or groundwater.
The manufacturing process of perforated HDPE pipes involves advanced techniques to ensure consistent hole spacing and size, which is crucial for optimal performance. These pipes can be fused together seamlessly, eliminating the risk of leaks common in traditional jointed pipes.
Despite these benefits, proper installation and maintenance are key to realizing the full potential of perforated HDPE pipes. Factors like soil type, perforation pattern, and pipe diameter must be carefully considered during planning to ensure efficient functioning.
In conclusion, perforated HDPE pipes, with their unique combination of strength, adaptability, and functional efficiency, have become an indispensable component in modern infrastructure. Their versatility and eco-friendly attributes make them a preferred choice for engineers and contractors worldwide, contributing significantly to sustainable development. As technology advances, we can expect even more innovative uses and improvements in perforated HDPE pipe design, further solidifying their position in the global piping industry.