Welding rods, also known as welding electrodes, play a crucial role in the welding process, serving as conductors of electricity and filler material to join metals together. They come in various types, each designed for specific applications, material types, and welding techniques.
One of the most common types is the Carbon Steel Welding Rod, typically used for welding mild steel due to its high carbon content. It's suitable for general-purpose repairs and construction projects. The E7018 is a popular choice within this category, offering excellent mechanical properties and low hydrogen content, making it resistant to cracking.
Stainless Steel Welding Rods, on the other hand, are used for welding stainless steels. They provide excellent corrosion resistance and are often used in food processing, chemical plants, and marine environments. The 308L and 316L grades are widely used, with 'L' indicating a lower carbon content to reduce the risk of intergranular corrosion.
Aluminum Welding Rods are ideal for welding aluminum and its alloys. They are non-ferrous and require alternating current (AC) or direct current with a negative electrode (DCEN) for successful welding. The 4043 and 5356 grades are commonly used, where 4043 is suitable for all-position welding while 5356 offers higher strength.
For welding cast iron, Cast Iron Welding Rods like the E6013 are used due to their ability to create a strong bond without cracking. These rods have a high carbon and low alloy content, making them ideal for repairing damaged or worn-out cast iron parts These rods have a high carbon and low alloy content, making them ideal for repairing damaged or worn-out cast iron parts
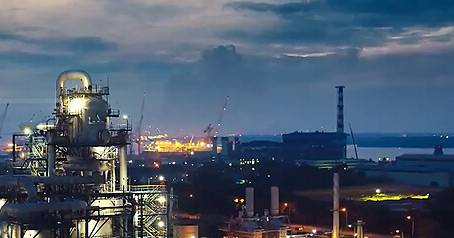
These rods have a high carbon and low alloy content, making them ideal for repairing damaged or worn-out cast iron parts These rods have a high carbon and low alloy content, making them ideal for repairing damaged or worn-out cast iron parts
welding rod types.
Tungsten Inert Gas (TIG) Welding Rods, or tungsten electrodes, are used in TIG welding. They do not melt during the welding process but provide the arc needed to heat the workpiece. Different tungsten types, such as pure tungsten, thoriated, and ceriated, are chosen based on the type of metal being welded and the desired arc characteristics.
MIG Welding Wire, though not a rod, is another type that deserves mention. It is fed continuously from a spool during the Metal Inert Gas (MIG) welding process. The wire's composition matches the base metal, ensuring a strong weld.
In conclusion, the selection of the right welding rod is critical for achieving a high-quality, durable weld. Each type has its unique properties, suited to different materials, welding methods, and environmental conditions. Understanding these differences allows welders to make informed decisions and execute their tasks effectively. Whether it's the robustness of carbon steel rods, the corrosion resistance of stainless steel, the adaptability of TIG, or the precision of MIG, the variety of welding rods ensures a solution for every welding need.