High-Density Polyethylene (HDPE) welding rods are essential components in the realm of plastic welding, particularly in industries focused on piping systems, fabrication, and repair. Their use ensures the creation of strong, sustainable joints between individual HDPE components, facilitating superior performance and durability. This article not only sheds light on the utility and application of HDPE welding rods but also strives to establish a comprehensive understanding of their properties and why they are indispensable in specific contexts.
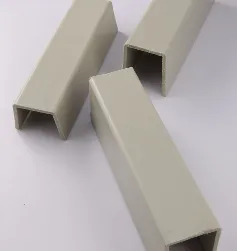
HDPE welding rods are a byproduct of HDPE resin, known for its excellent resistance to chemicals and moisture, making it an ideal material for welding. Given its popularity across numerous sectors, manufacturing processes have been optimized to enhance its viability and efficiency in welding applications. Unlike other plastic welding materials, HDPE possesses characteristics that make it impervious to severe weather conditions, which is pivotal for infrastructure projects exposed to environmental challenges.
When selecting HDPE welding rods, expertise in identifying quality materials is crucial. They should conform to stringent industry standards that ensure their reliability and effectiveness. This involves evaluating factors such as tensile strength, melting point, and flexibility. An experienced welding professional would recommend conducting a pre-check on the rods' consistency and diameter, ensuring they are compatible with the specific HDPE sheets or pipes intended for joining.
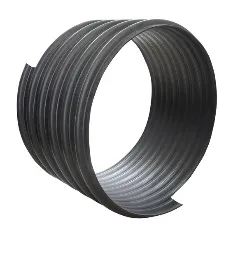
The welding process itself requires a high level of skill and understanding of HDPE's properties. Practitioners often use techniques such as extrusion welding, where HDPE rods are heated and extruded to form a solid, fused bond with the base material. This method demands precision, as the temperature and speed must be meticulously controlled to prevent defects in the weld seam. Mastery in this technique is demonstrative of a welder's expertise in handling HDPE materials, bolstering the credibility of the final construction or product.
hdpe welding rod
From an authoritative standpoint, HDPE welding rods are endorsed by numerous industry standards organizations, such as the American Society for Testing and Materials (ASTM) and international equivalents like the International Organization for Standardization (ISO). The endorsement from these reputable bodies underscores the rods' compliance with necessary safety, performance, and environmental sustainability criteria.
Trustworthiness in the use of HDPE welding rods extends to the transparency of their production and supply chain. Leading manufacturers adhere to eco-friendly practices, ensuring minimal environmental impact during production. Consumers seeking trustworthy sources should look for manufacturers with verifiable certifications in sustainable practices and quality management systems.
Real-world applications of HDPE welding rods span various sectors. In infrastructure, these rods are pivotal in assembling large-scale water supply and sewage systems due to their resistance to the corrosive nature of the materials being transported. The agricultural sector values HDPE welding rods for constructing durable irrigation frameworks. Furthermore, the automotive industry utilizes them for certain aspects of vehicle manufacturing, ensuring robust and long-lasting components.
In conclusion, HDPE welding rods are a cornerstone in any project requiring resilient plastic welding solutions. Their inherent properties and the meticulous standards governing their production reflect a broader commitment to sustainability, safety, and efficiency. Professionals in the welding industry value these rods not only for their technical capabilities but also for the peace of mind they provide through compliance with rigorous standards and environmentally conscious manufacturing. Whether for infrastructure, agriculture, or automotive applications, HDPE welding rods continue to affirm their essential role, driven by expertise and bolstered by a legacy of trust and authority.