HDPE sheets, often heralded as the robust backbone of a myriad of industrial and commercial applications, come in various sizes tailored to meet the specific needs of their diverse clientele. Understanding these sizes and their applications can significantly influence your purchasing decisions, leading to more efficient project execution and enhanced product longevity.
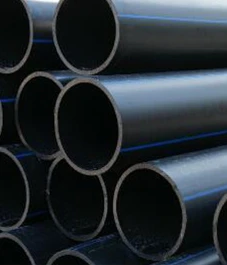
High-density polyethylene (HDPE) is revered for its remarkable strength-to-density ratio, making it a top choice for customers seeking durability without the cumbersome weight of other materials.
When selecting HDPE sheets, one of the foremost considerations is understanding the available sheet sizes and their corresponding uses.
Typically, HDPE sheets are available in standard sizes; however, custom sizes can be fabricated to address unique requirements. The industry-standard sizes usually include 48 inches by 96 inches (4 feet by 8 feet) and 60 inches by 120 inches (5 feet by 10 feet). These dimensions are optimal for a wide range of applications, from simple DIY projects to complex architectural endeavors. The thickness of these sheets usually varies from 1/16 inch to much thicker plates of 4 inches or more, offering options that cater to different levels of flexibility and strength.
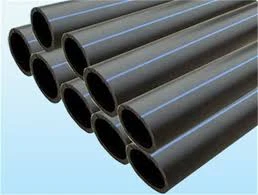
In practical terms, selecting the appropriate size is crucial for minimizing waste and ensuring cost-effectiveness on your part. For large-scale projects, opting for bigger sheets might reduce the need for multiple joins, enhancing the integrity and appearance of the finished product. Conversely, smaller sheets can be more manageable and easier to handle, especially for intricate designs or constrained spaces.
hdpe sheet sizes
For instance, industries like marine construction often favor thick HDPE sheets for dock fender pads, where resistance to harsh environmental conditions is critical. These applications typically require custom sizes beyond the standard to fit specific structures or designs accurately. On the other hand, the food processing industry might prefer thinner, standard-sized sheets for cutting boards, benefiting from HDPE’s non-porous surface, which resists bacterial growth.
Aside from standard and custom sizes, it’s vital to consider the method of production involved in HDPE sheets, which can impact their final dimensions and consistency. Generally, sheets are manufactured using either an extrusion or calendaring process, each offering different benefits in terms of size precision and surface texture. Those produced by extrusion might have tighter tolerances, facilitating better alignment and fit when multiple sheets are joined together.
Furthermore, understanding the relevance of sheet sizes in various sectors bolsters one's capability to select the precise dimensions best suited for their needs. Industries ranging from construction to automotive manufacturing rely on the adaptability of HDPE sheets’ sizes and shapes to innovate and enhance their processes. Hence, the knowledge of exact sizes contributes significantly to the efficiency of operations across different industries, ultimately leading to higher quality end products.
In summary, HDPE sheet sizes are more than just measurements; they are a reflection of versatility and purpose. Whether you are a seasoned professional in the industrial sector or an entrepreneurial DIY enthusiast, having an in-depth understanding of HDPE sheet sizes will empower you to select the right material for each project. Achieving the right balance between size, thickness, and application not only maximizes efficiency and performance but also ensures that your investment in HDPE materials yields the greatest possible return. As you delve deeper into your projects, keep these considerations in the forefront, and harness the transformational potential of HDPE’s diverse dimensional offerings.